Quality at mbw®
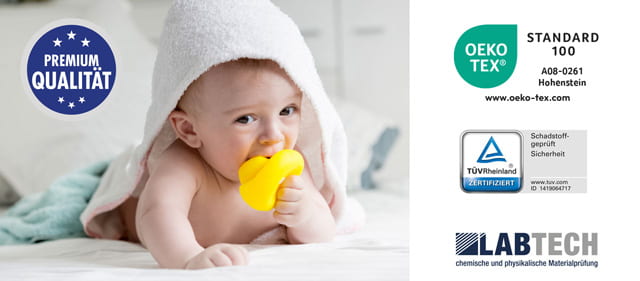
Each advertising medium also represents the advertising company. Against this background, the quality of the article used is particularly important, because the impression that the promotional item leaves is also transferred to the sender. In addition, good and secure advertising media also communicate appreciation towards the recipient - the basis for successfully initiating and cultivating customer contacts.
We not only adhere strictly to the requirements of the Toy Directive and the Product Safety Act (ProdSG), REACH and the legal requirements, in many cases we exceed them.
We regularly test the quality of all our products, among others by TÜV Süd, TÜV Rheinland, OEKO-TEX®, Labtech and other certified and accredited institutes.
Quality management at mbw®
Quality control in the Far East is carried out by employees who continuously monitor production and thus make an important contribution to ensuring that mbw® will continue to be able to supply selected products reliably and in consistent quality in the future.
Since July 2012, mbw® has installed an in-house quality management system. This department is solely responsible for product monitoring, compliance with guidelines and standards, and process optimization in the company. Within the context of quality management, a large number of BSCI factories in China are regularly visited. mbw® itself is amfori BSCI member since 2010.
This makes quality visible, tangible and measurable and creates trust.
Cuddling and advertising with quality
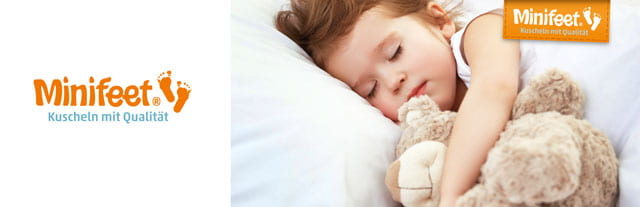
The orange MiniFeet® label from mbw® stands for cuddling with quality. Accordingly, mbw® is continuously committed to guaranteeing the exclusive quality and the best possible safety of the MiniFeet® articles.
Certified materials for advertising plush animals
At mbw®, only high-quality materials are used. All products comply with legal requirements. Many of them have been tested by renowned test institutes such as TÜV Rheinland, TÜV Süd or Eurofins.
The following aspects should generally be taken into account when using stuffed animals as an advertising medium:
- Are the eyes securely fastened?
- Are small parts removable?
- Are there any open seams?
- What's the smell?
- Does the material discolour?
- What is the material strength like?
- Is the cleanliness requirement fulfilled?
- Does the article have a product label?
Quality you can trust in
How a MiniFeet® teddy bear is made.
Using our Ralle teddy bear as an example, we show you how certified quality toys are made and which test procedures are used.
Design requirements
From the very first idea for a new product, the focus of our thoughts is on exceeding the legal requirements. We pay attention to the realisability and the choice of materials already at the design stage and make use of materials that have already been tested and certified.
Test labels and their meaning
The CE mark
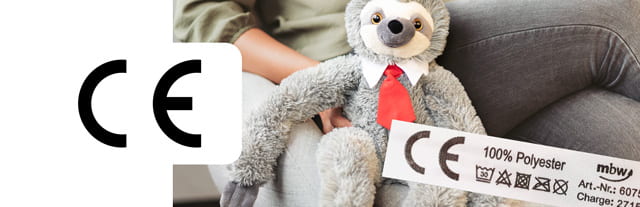
The safety of toys is the responsibility of the manufacturer/distributor. He confirms this by the CE mark, which he puts on the product himself.
The CE mark is considered a "passport" for the European market and an initial indicator of trustworthy products. It documents compliance with product-specific European directives. - in our case the EN71. For some products there is a CE marking duty, e.g. for electrical appliances, building products and also toys for children.
A CE conformity assessment is very complex and must be checked regularly. In the case of product improvements, this assessment must be done again.
Please note: The CE mark alone says nothing about the harmlessness of a product!
Manufacturers could also attach it to the product without prior testing. They would violate laws, standards and relevant directives and be liable to prosecution. Unfortunately, this is the case over and over again, which further lowers consumer confidence. Only a declaration of conformity confirms the legality of a CE marking.
Our tip for buying advertising material:
Ask for a declaration of conformity for all products with CE marking. This way you can also show your customers that product safety is close to your heart. The declaration of conformity is provided to you by mbw® free of charge.
The TÜV Proof Mark
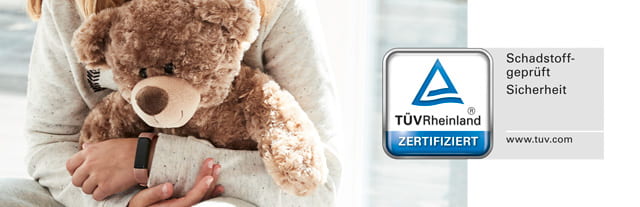
The TÜV Proof Mark is awarded to the tested product for one year after a comprehensive test of both physical-mechanical and chemical properties. In its tests, TÜV ensures that the toys tested not only comply with the EU standard DIN EN 71, but also subject each toy to an additional pollutant test. The audit firm examines whether the toys can withstand the usual stresses and strains of playing. In addition, there must be no risk of injury from cables, ropes, corners or detachable parts.
The TÜV-Proof test by TÜV Rheinland documents the quality, safety and usability of our products with a neutral and recognised test mark - quickly found on the online certification database using the unique identification number.
Labtech
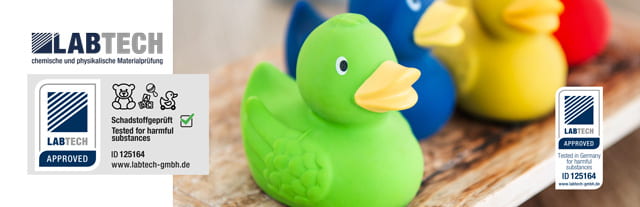
The LABTECH test mark confirms the high quality of our products. Through all standard-compliant physical and chemical tests and inspections, LABTECH Prüfgesellschaft mbH guarantees that all relevant pollutant regulations, such as REACH, are considered and complied with.
OEKO-TEX® Standard 100
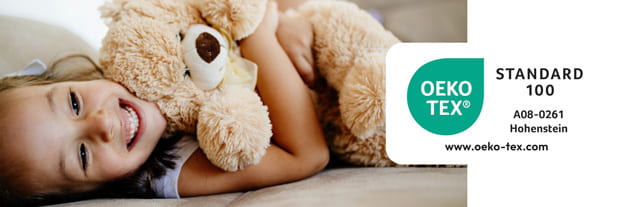
With its decades of experience, the OEKO-TEX® STANDARD 100 contributes to a high and effective product safety from the consumer's point of view. Test criteria and limit values often go far beyond national and international regulations. Extensive product controls and regular company audits also ensure that the industry is sensitized to the responsible use of chemicals in a sustainable manner throughout the world. Thanks to this concept, the OEKO-TEX® STANDARD 100 has been a pioneer for many years.
Textile products receive the STANDARD 100 label if they have been successfully tested for harmful chemicals on the basis of the comprehensive OEKO-TEX® criteria catalogue by one of the OEKO-TEX® member institutes and thus contribute to effective consumer protection. The prerequisite for the certification of products according to OEKO-TEX® STANDARD 100 is that all components of an article meet the required criteria without exception - in addition to the outer fabric, e. g. sewing threads, inlays, prints, etc., as well as non-textile accessories such as buttons, eyes, pellets, etc., for example.
STANDARD 100 test criteria: The OEKO-TEX® tests for harmful substances comprise more than 100 different parameters and go far beyond the legal requirements. These include, among others:
- Forbidden azo colorants
- Carcinogenic and allergenic dyes
- pesticides
- Heavy metals (e. g. nickel)
- Plasticizers (Phthalates)
- formaldehyde
The certified articles comply with the applicable requirements of Annex XVII of REACH. Comprehensive safety for the consumer - this is the claim of the OEKO-TEX® STANDARD 100 testing of harmful substances.